你知道组装一部手机需要多少个部件吗?你知道生产一部手机需要用多长时间吗?
你可能很难想像,原来组装一部手机,需要涉及多达1000个物料,100多道工序。
你是否能在脑海里描绘出这样一幅画面:整个生产基地,从大卡车向基地运货、物料自动仓储入库、生产线自动提取配件、成品出库,全线采取智能化管理。生产组装环节采用人机结合,机器完成大部分工作。整个生产制造流程,从一个零件的传输,到最后成品的运送,主要工作基本都是由机器人独立操作完成。
2015年,华为每条产线员工上百人,生产一部手机需要10分钟,而现在,只需17名工人,每28.5秒产出一台手机。
这个了不起的数字背后是国产制造技术的飞跃进步,中国速度的真实写照,更说明了生产自动化和智能化设备为制造产业带来的生产周期、质量和效率的同步改善,这是精细化成本管理和科技发展的成果。
据悉,2020年国内市场5G手机累计出货量1.63亿部,25年全球手机出货量有望达到15亿台(IDC预测,CAGR3.6%)。在如此大的市场体量下,这必然要求手机的生产、组装、检测等环节都有很高的自动化和智能化水平。
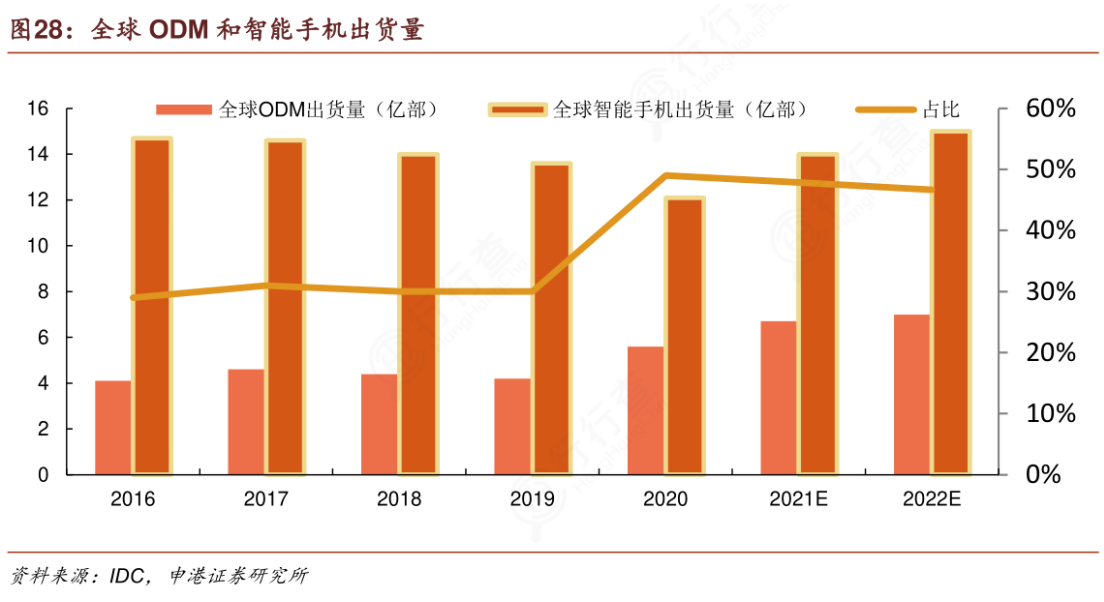
图片来源于行行查
为了确保手机组装的成品具备高可靠性,品质检测决定了每台手机的出厂身份证是否为“绿码”。
而手机缺陷检测,不仅有手机内部冲压件尺寸的精密测量、手机边框的点胶检测,还有手机外壳的污点划痕、手机外包装的字符识别等等,需要检测的缺陷种类繁多且复杂多变。使用检查、引导和识别性能的技术和装备来检测,就会让复杂的事情变得简单起来。
今天我们为大家列举3个手机检测案例,来呈现3D视觉检测在手机检测中的优势:
客户检测需求:
检测胶宽、胶高及断胶。
检测方法:
1、用3D轮廓仪扫描,对整体产品成像,以点胶接触底面建立基准面;
2、整个长胶路分成两个检测区域,使用轨迹检测工具进行胶路胶宽、胶高、断胶缺陷检测。
检测结果:
精确检测胶路宽度和高度信息判别点胶质量。
检测需求:
检测产品边缘高度。
检测方法:
1、用3D轮廓仪扫描,对整体产品成像;
2、选取产品中间任意N个区域为基准,拟合平面,计算边缘与平面之间的高度差。
检测结果:
重复性精度在0.01-0.02mm左右。
客户检测需求:
检测多种类型螺钉浮高。
检测方法:
1、用3D轮廓仪扫描,对产品整体成像,以产品边沿特征建立坐标系作定位;
2、用4个区域检测工具提取螺钉顶端区域,在螺钉周围用基准平面工具选取3个区域拟合基准面;
3、输出螺钉顶端到基准平面的段差 。
检测结果:
螺钉高度检测静态重复性为5um左右。
手机壳高度差3D检测示意
以上是昂视在手机制造业视觉解决方案中的小部分实例,在以往的项目中,昂视LP系列3D轮廓仪的不俗表现均获得客户广泛认可。
基于在机器视觉领域逾八年的丰富经验和雄厚研发功底,针对手机制造业不断更新的需求,昂视能为手机制造企业提供2D视觉、3D视觉及读码检测需求的整体解决方案,确保在手机生产环节应对如检测、对位、测量、OCR 以及一维和二维条码读取等种类繁多的检测,满足客户各种应用的精确要求。